Lakeview on the Rise – Affordable Multi-Family Housing Vision Brought to Life
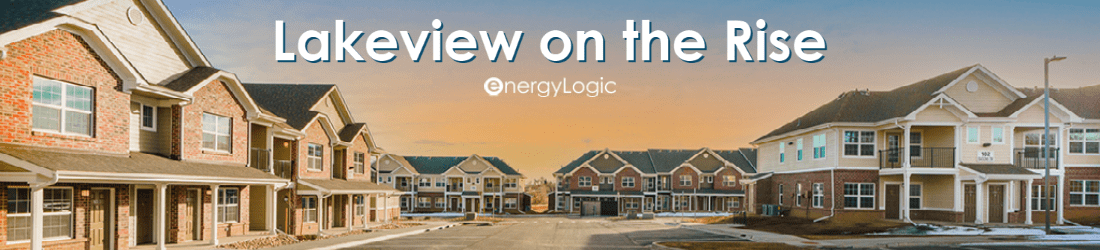
Multi-family experts share invaluable insights of their collaborative journey centered on premier indoor air quality and energy efficiency performance.
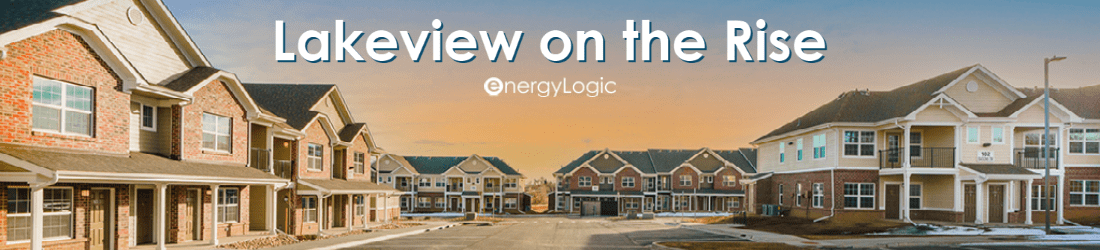
Published June 30, 2021
Eye on Luxury Living
Lakeview on the Rise boasts 20 acres of amenity living with 17 new two-story apartment buildings, providing 180 spacious energy-efficient apartment units. Located in vibrant Fort Collins, Colorado, a college town recently named "Best Place to Live in America," the community features an envious clubhouse with fitness and business centers on-site, a pool, a playground, and a pelican viewing pavilion for all residents to enjoy. Signature Construction has outdone themselves with this luxury, affordable Housing and Urban Development (HUD) project!
Signature Construction, EnergyLogic, and Northern Colorado AeroBarrier, among other industry professionals, set out to increase efficiency measures, knowing there would be a few hurdles along the way to achieve tighter compartmentalization of the units. These measures addressed a variety of indoor air quality issues, comfort, and noise, all significant factors for builders and occupants in multi-family buildings. Hear from the team of building science experts who shared their experience, lessons learned, and critical project milestones along the journey.
Project Q&A
Why is the compartmentalization of units essential and present in all housing levels, particularly in multi-family buildings?
Compartmentalization of homes and dwelling units has become increasingly critical as building science knowledge increases. Designing and installing effective air sealing details to separate the living spaces from outside and other potential living or shared spaces helps regulate and reduce energy uses. Furthermore, it helps with air pollutants, noise, and comfort throughout the home or dwelling unit by minimizing air transfer to the outside and between units. These features also aid in the longevity of buildings by keeping harmful air source materials out of the homes and dwelling units and helping with potential mold issues.
Effective air sealing and compartmentalization are especially critical in multi-family buildings because of the opportunity for air pollutants and noise to be easily transferred between separate apartments if installed incorrectly. It also helps offset the effects of unknown occupancy behaviors.
In multi-family buildings, where the behavior of our neighbors can directly affect our living environment, compartmentalization helps to further mitigate against the adverse effects of those behaviors. The most obvious example of this is when someone is smoking or cooking strong-smelling dishes and the odor is detected in the adjacent units. However, compartmentalization helps with comfort and energy consumption as well. By effectively separating and compartmentalizing the units from each other, the temperature differences between units will not drive energy transfer. To put it simply, your neighbors' thermostat setting will not affect you as much if compartmentalization between units is completed. In addition, with the outbreak of COVID-19, the ability to stop transmission of air-borne illnesses by effective compartmentalization has become a focus.
What are some of the key benefits of building to high-performing standards by using processes and products to optimize healthy indoor air quality?
Prioritizing indoor air quality has become increasingly crucial as indoor air pollutants and harmful particulate transmission are understood. As Volatile Organic Compounds (VOCs) find their way into more building materials, they become measurable in the occupied home later. In multi-family buildings, like Lakeview on the Rise, these air sealing processes and products are even more critical where neighbors' habits and illnesses can be easily transmitted. When the health of the occupants is maintained, you see an overall positive impact on society.
It's important to remember that once such tightly sealed units are achieved, there are still ventilation requirements that must be met. Although the American Society of Heating, Refrigerating and Air-Conditioning Engineers (ASHRAE) has differing targets based on the adoption year, we must ensure the performance of applicable ventilation systems to deliver fresh air. When there are competing ventilation systems in units sharing common walls, there is a high potential to transfer stale air from one unit to the next. Isolating each unit ensures the ventilation systems are not experiencing cross-over through common walls. This will also reduce perceived odors from everyday activities like cooking.
We now have the ability to control the compartmentalization through air infiltration mitigation in buildings. This makes it easier than ever to deliver the best possible product to the end client. For Lakeview on the Rise, the units will be compartmentalized, as well as affordable. Adding this layer of accountability to the building process also provides lower cost to the end-user, as well as to the builder. It will be very interesting to see if Signature will see a saving on the warranty side of this building after doing such a great job of compartmentalizing the units with Northern Colorado AeroBarrier.
What were some of the significant challenges of this project?
This project opted to sample the final inspections of the units. Sampling involves testing a percentage of units to verify and certify the entire project. For Lakeview on the Rise, they had to test and pass 20% or 1/5 units per building. This process has multiple benefits from a cost and scheduling standpoint in that it typically requires fewer field inspections by the Energy Rater. However, there are many potential issues if effective coordination and planning between all teams do not occur. Sampling involves randomly selecting units to inspect at the final and ensures the builder cannot focus on specific units. This means trades must maintain quality work throughout the entire project. Having AeroBarrier sealing all units assured the blower door part of the final inspection would never be an issue.
Meeting jurisdictional air leakage requirements on a project like this is not easy. Colorado has a variety of air infiltration requirements based on the jurisdiction that the home is built in. This makes it difficult for builders and trades to be aware of the requirements consistently and meet them. Furthermore, multi-family units designed with party or adiabatic walls are notorious for inadequate air sealing details and processes to mitigate air being transferred between apartments effectively.
Why? What are the most common Issues?
Typically, the issues arise from a design standpoint and when air sealing experts are brought onto a project late. It is critical that the air sealing details make it into the plans and that everyone from the architect to field contractors understand the scope of those details before framing begins.
Tarik Simmons, COO with Northern Colorado AeroBarrier, explained just how important this step is in the process.
This is a common problem we experience within our industry. Builders are often left feeling helpless when they find out that their building envelope is not adequate. We see a lot of finger-pointing when we come to help these builders. The inspectors say it's the builders; the builders say it's the trades, the new codes, and so on. Like most things in building, it's not just one person's inability. Builders, architects, and trades all have a role to play, and it should start with planning to build the best building possible regardless of code-driven designs. Design and build better than code; it's that simple!
How does the AeroBarrier product impact performance results compared to traditional air sealing methods?
"Having AeroBarrier as a partner gave us reassurance that the units would be well-sealed and compartmentalized at the final inspection phase," said DeWolfe.
Traditional air sealing methods have a group of guys go around an entire building and caulk everything they can. This process is inefficient and ineffective. At the end of the day, after all those guys are done caulking everything, the builder is still left not knowing but hoping it was good enough. AeroBarrier takes the guesswork out of knowing your project has been properly air sealed. Northern Colorado AeroBarrier works with all of our clients throughout the entire building process to ensure the synergy between everyone involved focuses on providing the best possible airtightness for the building.
Signature Construction's Superintendent, Taylor Elizalde, shared his insight on the project, commenting: "AeroBarrier has definitely proven to be an efficient product at Lakeview. We've easily passed all our final blower door tests throughout the entire project. It was a quick and effortless application throughout, which allowed us to stay on or ahead of schedule."
Identifying what works, what doesn't, and what is most cost-effective ensures quality is not compromised.
Why is AeroBarrier not the 'ultimate fix' for air sealing in units? Why was a collaboration amongst all parties involved important, and how did this impact the project's success?
Active participation amongst all parties is required to ensure the AeroBarrier product is and remains effective. Collaboration between EnergyLogic, Signature Construction field staff, AeroBarrier, construction trades, and the overall construction schedule requires excellent communication and coordination.
Additionally, an upfront focus on what air sealing details should be covered by the trades and what is eventually to be sealed by the AeroBarrier product are critical components to achieve productive air sealing field inspections. Identifying which air sealing components are planned for installation at the beginning of the project and which the builder would forego, knowing AeroBarrier would seal, provided EnergyLogic's field team with the necessary tools to effectively inspect the units without having to call for reinspections for missing details.
We are not in the business of selling snake oil to anyone. We are builders and subcontractors working to be better at what we do. Northern Colorado AeroBarrier are general contractors themselves and got into the business of air sealing because we recognized two major points. 1) Air sealing is important. If you don’t think so, we can’t help you. 2) Air sealing a building is extremely hard. We finally have the technology that makes air sealing a building easier, but it still takes a forward-thinking plan to implement what we do. Without a plan around what your building’s airtightness needs to be, you’ll be aiming blind with or without AeroBarrier.
A Data-Driven Tale
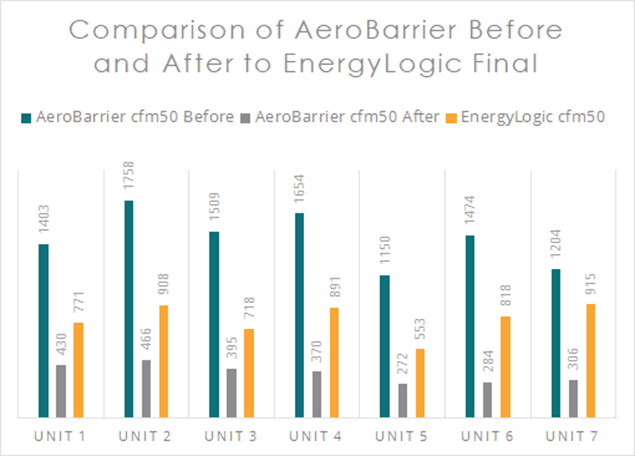
Data supports an upward trend in increased air infiltration post-AeroBarrier application.
The above table shows pre-AeroBarrier infiltration results, post-AeroBarrier application infiltration results, and the subsequent final test by EnergyLogic infiltration.
- The average air leakage or infiltration rate before the application of AeroBarrier was over 1400cfm, with many units coming in over 10ACH before AeroBarrier application.
- The average air leakage or infiltration after applying the AeroBarrier product was 360cfm, or about 1.5ACH per unit.
- The average final air infiltration measured by EnergyLogic was 796cfm, showing a significant increase in infiltration rates between AeroBarrier application and final testing.
This knowledge demonstrated that most of the gap in leakage rates came from the AeroBarrier material being removed or additional penetrations being created after application. This insight highlighted the importance of buy-in and coordination among all trades and field staff.
A helpful hint to all builders: Build your mechanical closets better and hold HVAC trades to a higher standard. This is not me pointing fingers at the HVAC contractors out there. It’s a look into a trade that needs the ability to run their system through walls in order to make the building work. There are many trades like this, and if they all understood the importance of compartmentalization, especially in multi-family projects, we would see a significant increase in the effectiveness of a good building plan and execution.
Although AeroBarrier appeared to be the magic bullet, it was still important to have buy-in from the various trades touching these units to understand the final goal. It's important to remember that uninformed trades can remove the AeroBarrier product before final infiltration testing. As jurisdictional infiltration testing becomes more widely adopted, we need to make sure we include all trades not traditionally involved in air sealing to understand the importance of the end game and help everyone understand their impact along the way. Simply moving a light fixture can cause enough additional air leakage to fail local code requirements on units this small.
AeroBarrier was able to seal these units tight enough that the differences in our test results did not affect passing the final inspections. Further, by avoiding and decreasing the number of reinspections and the cost of materials for some of the air sealing details, the builder could pass these savings on to AeroBarrier and other project areas.
Matt Boyle, Project Manager of Pedcor Construction Management, parent company to Signature Construction, says:
It takes the headache out of things like constant re-caulking and worrying about passing. Although the product is expensive, I would likely have spent as much (or more) time and money on the additional caulking and re-caulking in the end. Most importantly, we would have failed units and had to rework and retest, causing a negative impact on the schedule.
Boosting Affordability in the Community
Lakeview on the Rise provides a positive community impact by providing new low-income HUD housing in a desired market. It did so to meet project-specific financing requirements with added environmental energy programs, including ENERGY STAR® and Enterprise Green Communities (EGC) certifications. By adding these programs and meeting the Fort Collins energy code, the builder guaranteed that this project will provide sustainable, efficient, and healthy homes for years to come.
This project is a HUD project intended for folks who really need affordable housing. In this case, the air leakage metric in the local jurisdiction was stringent. Meeting these goals set this project apart from other HUD projects that may be built faster but with less attention to detail. By building these units right the first time, we've ensured this project will be future-proof and maintain high-performance outcomes longer than the average apartment complex. This allows Lakeview on the Rise to have a longer-lasting community impact right where it's needed
Results That Give Back
By establishing clear goals and processes at the start of the project design and construction phase, we were able to identify necessary air sealing details and those that could be eliminated from the design, knowing that AeroBarrier would seal these areas. This provided EnergyLogic and Signature Construction field professionals with the tools and knowledge to successfully build and inspect units with fewer interruptions to the pre-drywall rough inspection schedule and reducing air sealing materials and costs. These results saved time and money on the project by eliminating blower door reinspections which is uncommon in multi-family projects.
Because of its success, this strategy and process are being used on future Signature Construction projects throughout Colorado in partnership with EnergyLogic and AeroBarrier.
Free Resource! Multi-Family Unit Compartmentalization White Paper
The nature of the construction techniques, sequencing, and trade training all make for a very challenging environment to achieve targeted separation levels. This white paper was created to help industry professionals:
- Understand why multi-family Unit Compartmentalization is important
- Identify the challenges of achieving targeted performance
- Explore the approaches currently available for compartmentalization
Authored by Steve Byers, CEO at EnergyLogic and Managing Director at EnergyPro Exchange (EPX), considerable assistance from EPX member Building Knowledge Canada and input from EPX member SK Collaborative.